Exploring the Brilliance of Compression Molding Companies
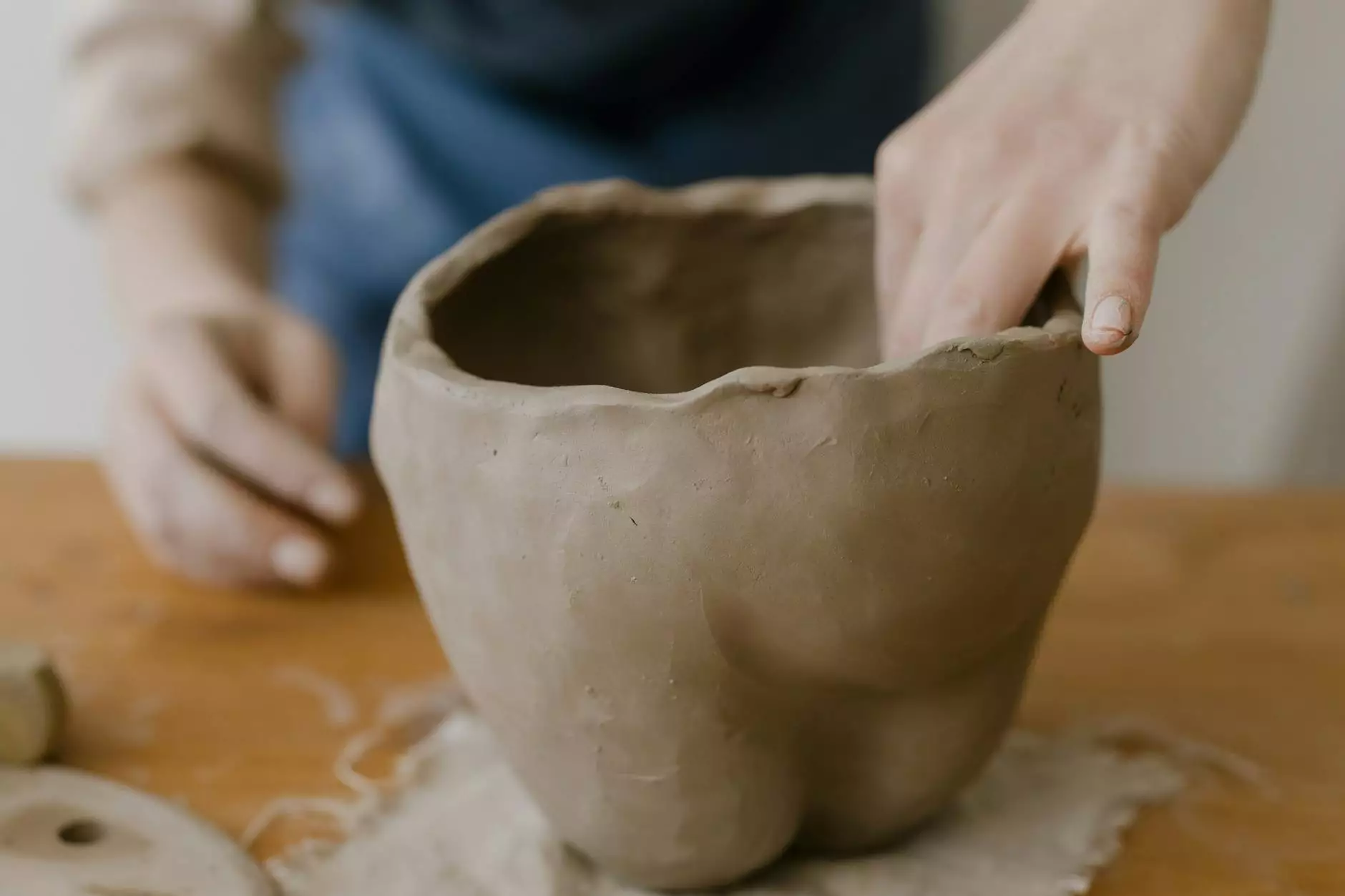
In today’s dynamic manufacturing landscape, compression molding companies have emerged as vital players, particularly in industries such as electronics and medical supplies. This revolutionary manufacturing process offers unparalleled benefits, including efficiency, cost-effectiveness, and superior product quality. Let's dive deep into the world of compression molding, shedding light on its processes, applications, and the exemplary role of companies like Nolato in shaping these industries.
What is Compression Molding?
Compression molding is a manufacturing process that involves placing a pre-measured amount of material, typically thermosetting plastics, into a heated mold. The mold is then closed, applying pressure to form the desired shape. This process is particularly advantageous for producing intricate parts with a high degree of accuracy.
Key Advantages of Compression Molding
- Cost Efficiency: Compared to other molding techniques, such as injection molding, compression molding generally incurs lower tooling costs. This makes it an attractive choice for mass production.
- Versatility: Compression molding is suitable for a wide range of materials, including rubber and thermoplastics, expanding its application scope across various industries.
- Reduced Waste: The process minimizes scrap material, as there is less waste generated compared to traditional machining methods.
- High Strength: Products manufactured through compression molding exhibit excellent tensile strength, making them ideal for demanding applications.
Applications in the Electronics Industry
In the fast-evolving electronics industry, the demand for lightweight yet durable components is ever-growing. Compression molding companies, like Nolato, excel in creating parts that meet these specifications while ensuring compliance with stringent quality standards.
Custom Components for Electronic Devices
Compression molding allows for the production of custom components that are essential for various electronic devices. These include:
- Connectors: Crucial for establishing links between different electronic systems, connectors manufactured through compression molding are reliable and robust.
- Enclosures: The protective outer shells for devices, often manufactured from specialized polymers that enhance durability and aesthetic appeal.
- Insulators: Essential for preventing unwanted electrical conductivity, these components can be engineered to support specific voltage requirements.
Transforming Medical Supplies through Compression Molding
The medical supplies sector demands precision and reliability. Compression molding companies play a pivotal role in ensuring that medical devices are not only cost-effective but also meet stringent health and safety regulations.
Creating Reliable Medical Devices
With the increasing demand for enhanced medical technologies, companies like Nolato invest in advanced compression molding techniques to produce:
- Surgical Instruments: High-quality, durable instruments that can withstand autoclaving processes without losing integrity.
- Diagnostic Equipment: Precision components that enhance the effectiveness of diagnostic tools.
- Medical Packaging: Safe, sterile packaging solutions that ensure the longevity and safety of medical products.
The Compression Molding Process Explained
The compression molding process involves several key stages:
1. Material Preparation
Materials, typically in the form of granules or powder, are prepared for the molding process. Additives may be included to enhance specific properties, such as strength or flexibility.
2. Molding Process
A pre-measured amount of material is placed into the open mold. The mold is then closed, and heat and pressure are applied. The combination of these factors causes the material to flow and fill the mold cavity.
3. Cooling and Demolding
After the appropriate curing time, the mold is cooled, and the finished product is carefully removed. This stage ensures the integrity and dimensional accuracy of the part.
Choosing the Right Compression Molding Company
When it comes to selecting a compression molding company, there are several factors to consider:
- Experience: A company with a solid track record in your specific industry will be better equipped to meet your needs.
- Technology: Look for companies that utilize the latest molding technologies and quality control measures.
- Keen Understanding of Regulations: Especially important in sectors like medical and aerospace, a thorough knowledge of industry regulations is crucial.
- Scalability: Choose a company that can scale production up or down based on your requirements without compromising quality.
Future Trends in Compression Molding
The future of compression molding looks promising as technology continues to advance. Here are some expected trends:
1. Enhanced Materials
As new materials are developed, the versatility of compression molding will expand, allowing for novel applications in diverse sectors.
2. Automation and Industry 4.0
Increased automation in the molding process will enhance efficiency and reduce production times, while smart factories will optimize operations through data analytics.
3. Eco-Friendly Practices
Environmental sustainability will become a key focus, with companies seeking to utilize recycled materials and more energy-efficient processes.
The Role of Nolato in Compression Molding
Nolato stands as a beacon of excellence in the realm of compression molding companies. Known for its commitment to quality, innovation, and sustainability, Nolato caters to numerous industries, providing comprehensive solutions that meet varied demands.
Commitment to Quality
Nolato prioritizes exceptional quality control across all manufacturing stages, ensuring that each product not only meets but exceeds industry standards.
Innovative Solutions
With a dedicated team of professionals, Nolato leverages the latest technological advancements to create state-of-the-art products that cater to the evolving needs of electronics and medical supplies.
Sustainability Initiatives
Nolato is also at the forefront of implementing sustainability initiatives, focusing on reducing environmental impact through responsible sourcing and energy efficiency.
Conclusion
In summary, compression molding companies play an indispensable role in the modern manufacturing landscape, especially within the electronics and medical supplies industries. Companies like Nolato exemplify how innovation, quality, and sustainability can coalesce to produce exceptional products that enhance everyday life. As we move forward into a future defined by rapid technological advancements, the significance of compression molding will undoubtedly continue to grow, offering exciting possibilities for both manufacturers and consumers alike.
With benefits like cost efficiency, versatility, and reliable quality, now is an excellent time for businesses to consider partnering with reputable compression molding companies to meet their production needs.